 |
 |
 |

DHS ELEKTON-TMS-12 Telemetry System for downhole applications
|
|
Fig.1
1- ESP submersible cable
2- Tubing
3- Pump sections
4- Protector,equalizer
5- ESP motor
6- TMS-DHS-12 downhole unit with sensors
for measurement of:
- formation fluid pressure;
- formation fluid temperature;
- ESP motor oil temperature;
- ESP motor stator temperature (optional);
- vibration acceleration (optional).
|  |
 |
Purpose and field of application |  |
|
ELEKTON-TMS-12 is designed for normal completions, its main field of application: automation
of electric drive operating modes for oil production equipment. ELEKTON-TMS-12 downhole
telemetry system is designed to control, record and transmit to external devices current values
of the following parameters:
- ESP motor oil temperature;
- formation fluid temperature;
- ESP motor stator temperature measured by a separate sensor;
- ESP motor oil pressure;
- vibration along X, Y and Z axes (if respective sensors are installed);
- insulation resistance of the circuit "neutral point of step-up transformer HV star-connected
winding – ESP cable – neutral point of ESP motor star”.
The system remains operative with the cable length up to 6000 m.
The system supports universal Transfer v. 1 protocol for data exchange between the surface and
downhole components, as well as between the surface panel and the VSD controller.
Specific features and additional functionality of the ELEKTON-TMS-12 downhole telemetry
system:
- Low power consumption by the downhole sensor this optimizes operating temperatures
of the unit and increases reliability at high ambient temperatures.
- It is possible to determine in which part of the downhole unit the insulation resistance
dropped to zero: in the TMS-DHS itself or in the cable-ESP motor circuit.
- Increased speed and noise immunity of the data link.
- Information (commands) can be transmitted from the surface panel to the DHS, including
during ESP operation. This allows to control the operation modes of the downhole sensor
in real-time (selective data transfer, service information request, solenoid valve control, etc).
Selective data transfer allows, for example, receiving the pressure readings at the pump
suction more frequent than formation fluid temperature readings.
- The surface unit has a built-in USB-host and USB Type-A connector which makes it possible
to use virtually any flash drive to copy the event log and update internal software.
- Software of the surface unit can be updated via the USB connector of the ELEKTON-10.1
controller.
- The surface panel has two analogue inputs for the connection of external sensors, e.g.
wellhead pressure sensors.
Parameters |
System's overall dimentions, mm, max |
Weight of system units, kg, max |
TMS-SP-12 surface panel |
245х205х168 |
6 |
TMS-DHS-12 downhole sensor |
Ø=96, L=572,5 |
17,33 |
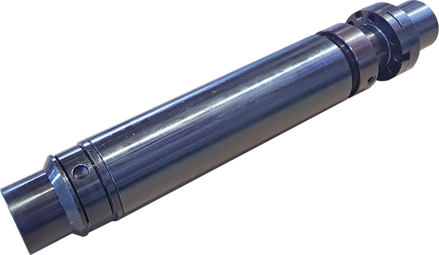
ELEKTON-TMS-DHS-12
|
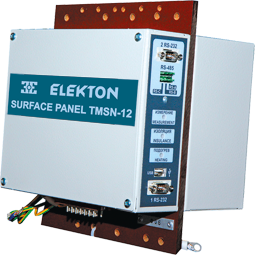
ELEKTON-TMS-SP-12 |
|
|
|
 |
|
|
|
 |
 |
Parameter range and measurement accuracy |  |
|
Parameter |
Range |
Accuracy1) |
Tolerance |
Formation fluid pressure at pump intake, PSI 1) |
0-5880, 0-8800 |
±0,5% |
0,001PSI |
ESP motor oil temperature, °C |
0-200 |
±1,5% |
0,01°С |
Formation fluid temperature at pump intake,°C |
0-200 |
±1,5% |
0,01°С |
ESP motor stator temperature measured by separate sensor, °C |
0-200 |
±1,5% |
0,01°С |
ESP motor vibration acceleration in radial and axial directions, m/s2 2) |
0-30 |
5%2) |
0,1m/s2 |
Insulation resistance, kOhm3 |
10-9999 |
±5% |
1kOhm |
VAC in the common point of the DHS HV winding, actual value, V |
50-2000 |
±10% |
10V |
Notes:
1) Allowable annual pressure drift – no more than 1%;
2) For the vibration acceleration range from 10 to 70 Hz, if the respective sensors are available;
3) Insulation resistance is measured by the surface unit.
|
|
|
|
 |
| |
RANGE of PRODUCTS
|  |